مقناطیس کیا ہے؟
مقناطیس ایک ایسا مواد ہے جو دوسرے مواد کے ساتھ جسمانی رابطے کے بغیر اس پر واضح قوت لگاتا ہے۔ اس قوت کو مقناطیسیت کہتے ہیں۔ مقناطیسی قوت اپنی طرف متوجہ یا پیچھے ہٹا سکتی ہے۔ زیادہ تر معلوم مواد میں کچھ مقناطیسی قوت ہوتی ہے، لیکن ان مواد میں مقناطیسی قوت بہت کم ہوتی ہے۔ کچھ مواد کے لیے مقناطیسی قوت بہت زیادہ ہوتی ہے، اس لیے ان مواد کو میگنےٹ کہا جاتا ہے۔ زمین خود بھی ایک بہت بڑا مقناطیس ہے۔
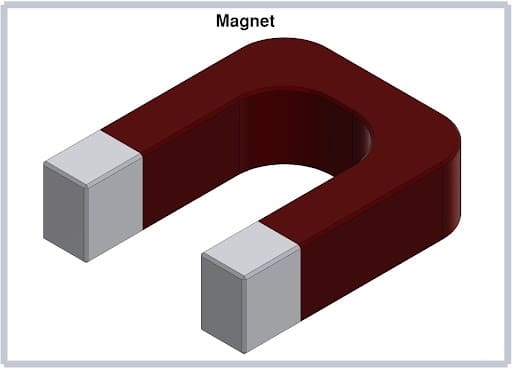
تمام میگنےٹس پر دو پوائنٹس ہیں جہاں مقناطیسی قوت سب سے زیادہ ہے۔ وہ کھمبے کے نام سے جانے جاتے ہیں۔ ایک مستطیل بار مقناطیس پر، کھمبے براہ راست ایک دوسرے کے پار ہوتے ہیں۔ انہیں قطب شمالی یا شمالی تلاش کرنے والا قطب اور جنوبی قطب یا جنوب کی تلاش میں کہا جاتا ہے۔
ایک مقناطیس صرف موجودہ مقناطیس کو لے کر اور اس کے ساتھ دھات کے ٹکڑے کو رگڑ کر بنایا جاسکتا ہے۔ استعمال ہونے والے اس دھات کے ٹکڑے کو ایک سمت میں لگاتار رگڑنا چاہیے۔ اس سے دھات کے اس ٹکڑے میں موجود الیکٹران ایک ہی سمت میں گھومنے لگتے ہیں۔ برقی رو بھی مقناطیس بنانے کی صلاحیت رکھتا ہے۔ چونکہ بجلی الیکٹرانوں کا ایک بہاؤ ہے، اس لیے جب موبائل الیکٹران کسی تار میں حرکت کرتے ہیں تو وہ اپنے ساتھ وہی اثر لے جاتے ہیں جو الیکٹران ایٹم نیوکلئس کے گرد گھومتے ہیں۔ اسے برقی مقناطیس کہتے ہیں۔
ان کے الیکٹرانوں کو ترتیب دینے کے طریقے کی وجہ سے، دھاتیں نکل، کوبالٹ، لوہا اور سٹیل بہت اچھے میگنےٹ بناتی ہیں۔ یہ دھاتیں میگنےٹ بننے کے بعد ہمیشہ کے لیے میگنےٹ رہ سکتی ہیں۔ اس طرح نام ہارڈ میگنےٹ لے کر جانا۔ تاہم یہ دھاتیں اور دیگر عارضی طور پر میگنےٹ کی طرح برتاؤ کر سکتی ہیں اگر وہ بے نقاب ہو جائیں یا سخت مقناطیس کے قریب آئیں۔ پھر وہ نام نرم میگنےٹ لے جاتے ہیں۔
مقناطیسیت کیسے کام کرتی ہے۔
مقناطیسیت اس وقت ہوتی ہے جب الیکٹران نامی چھوٹے ذرات کسی طرح حرکت کرتے ہیں۔ تمام مادہ ایٹموں کہلانے والی اکائیوں پر مشتمل ہوتا ہے، جو بدلے میں الیکٹران اور دوسرے ذرات پر مشتمل ہوتے ہیں، جو نیوٹران اور پروٹون ہوتے ہیں۔ یہ الیکٹران نیوکلئس کے گرد گھومتے ہیں، جس میں اوپر بیان کردہ دیگر ذرات ہوتے ہیں۔ چھوٹی مقناطیسی قوت ان الیکٹرانوں کی گردش کی وجہ سے ہوتی ہے۔ کچھ معاملات میں، آبجیکٹ میں بہت سے الیکٹران ایک سمت میں گھومتے ہیں. الیکٹرانوں سے ان تمام چھوٹی مقناطیسی قوتوں کا نتیجہ ایک بڑا مقناطیس ہے۔
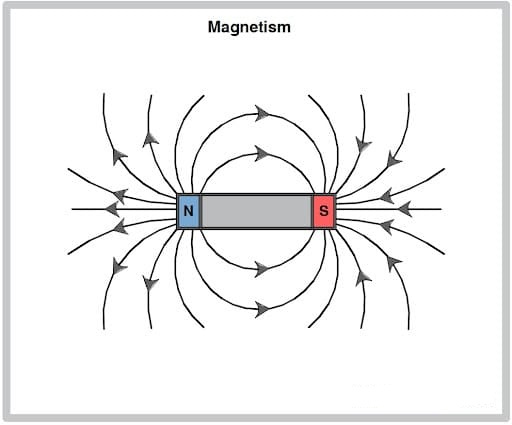
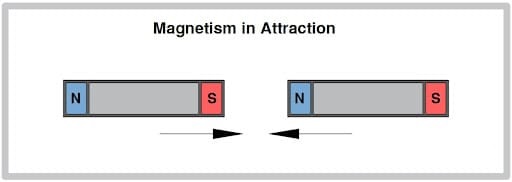
پاؤڈر کی تیاری
مناسب مقدار میں آئرن، بوران، اور نیوڈیمیم کو خلاء کے نیچے یا انارٹ گیس کا استعمال کرتے ہوئے انڈکشن پگھلنے والی بھٹی میں پگھلنے کے لیے گرم کیا جاتا ہے۔ ویکیوم کا استعمال پگھلنے والے مواد اور ہوا کے درمیان کیمیائی رد عمل کو روکنا ہے۔ جب پگھلا ہوا مرکب ٹھنڈا ہو جاتا ہے، تو یہ ٹوٹ جاتا ہے اور کچل کر دھات کی چھوٹی پٹیاں بناتا ہے۔ اس کے بعد چھوٹے چھوٹے ٹکڑوں کو باریک پاؤڈر بنا کر کچل دیا جاتا ہے جس کا قطر 3 سے 7 مائکرون ہوتا ہے۔ نیا بننے والا پاؤڈر انتہائی رد عمل والا ہے اور ہوا میں اگنیشن پیدا کرنے کے قابل ہے اور اسے آکسیجن کی نمائش سے دور رکھا جانا چاہیے۔
اسوسٹیٹک کومپیکشن
isostatic compaction کے عمل کو پریسنگ بھی کہا جاتا ہے۔ پاؤڈر دھات کو لے کر ایک سانچے میں رکھا جاتا ہے۔ اس مولڈ کو ڈائی بھی کہا جاتا ہے۔ پاؤڈر شدہ مواد کو پاؤڈر کے ذرات کے مطابق بنانے کے لیے ایک مقناطیسی قوت کا استعمال کیا جاتا ہے، اور مقناطیسی قوت کو لاگو کرنے کے دوران، ہائیڈرولک ریموں کا استعمال اسے مکمل طور پر اس کے منصوبہ بندی کے 0.125 انچ (0.32 سینٹی میٹر) کے اندر کمپریس کرنے کے لیے کیا جاتا ہے۔ موٹائی ہائی پریشر عام طور پر 10,000 psi سے 15,000 psi (70 MPa سے 100 MPa) تک استعمال ہوتے ہیں۔ دیگر ڈیزائن اور شکلیں مادوں کو گیس کے دباؤ سے مطلوبہ شکل میں دبانے سے پہلے ایئر ٹائٹ خالی کنٹینر میں ڈال کر تیار کی جاتی ہیں۔
مثال کے طور پر لکڑی، پانی اور ہوا لینے والے زیادہ تر مواد میں مقناطیسی خصوصیات ہیں جو بہت کمزور ہیں۔ میگنےٹ ان چیزوں کو اپنی طرف متوجہ کرتے ہیں جن میں سابقہ دھاتیں بہت مضبوطی سے ہوتی ہیں۔ جب وہ قریب لائے جاتے ہیں تو وہ دوسرے سخت مقناطیسوں کو بھی اپنی طرف متوجہ یا پیچھے ہٹاتے ہیں۔ یہ نتیجہ ہے کیونکہ ہر مقناطیس کے دو مخالف قطب ہوتے ہیں۔ جنوبی قطب دوسرے مقناطیس کے شمالی قطبوں کو اپنی طرف متوجہ کرتے ہیں، لیکن وہ دوسرے جنوبی قطبوں کو پیچھے ہٹاتے ہیں اور اس کے برعکس۔
مینوفیکچرنگ میگنےٹ
میگنےٹ کی تیاری میں استعمال ہونے والا سب سے عام طریقہ پاؤڈر میٹالرجی کہلاتا ہے۔ چونکہ میگنےٹ مختلف مواد پر مشتمل ہوتے ہیں، اس لیے ان کی تیاری کے عمل بھی اپنے طور پر مختلف اور منفرد ہوتے ہیں۔ مثال کے طور پر، برقی مقناطیس دھاتی کاسٹنگ تکنیک کا استعمال کرتے ہوئے بنائے جاتے ہیں، جب کہ لچکدار مستقل میگنےٹ پلاسٹک کے اخراج کے عمل میں تیار کیے جاتے ہیں جس میں خام مال کو شدید دباؤ کے حالات میں کھلنے سے پہلے گرمی میں ملایا جاتا ہے۔ ذیل میں مقناطیس کی تیاری کا عمل ہے۔
میگنےٹ کے انتخاب کے تمام اہم اور اہم پہلوؤں کو انجینئرنگ اور پروڈکشن دونوں ٹیموں کے ساتھ زیر بحث لایا جانا چاہیے۔ میگنےٹ کے مینوفیکچرنگ کے عمل پر میگنیٹائزنگ کا عمل، اس مقام تک، مواد کمپریسڈ دھات کا ایک ٹکڑا ہے۔ اگرچہ اسے آئسوسٹیٹک دبانے کے عمل کے دوران مقناطیسی قوت پر استعمال کیا گیا تھا، لیکن یہ قوت مواد پر مقناطیسی اثر نہیں لاتی تھی، اس نے صرف ڈھیلے پاؤڈر کے ذرات کو قطار میں کھڑا کیا تھا۔ اس ٹکڑے کو ایک مضبوط برقی مقناطیس کے کھمبوں کے درمیان لایا جاتا ہے اور اس کے بعد اس سمت کی طرف موڑ دیا جاتا ہے جس کا مقصد میگنیٹائزیشن ہوتا ہے۔ برقی مقناطیس کے متحرک ہونے کے بعد، مقناطیسی قوت مواد کے اندر مقناطیسی ڈومینز کو سیدھ میں لاتی ہے، جس سے ٹکڑے کو ایک بہت مضبوط مستقل مقناطیس بن جاتا ہے۔
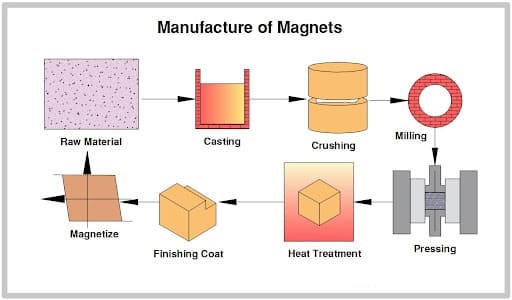
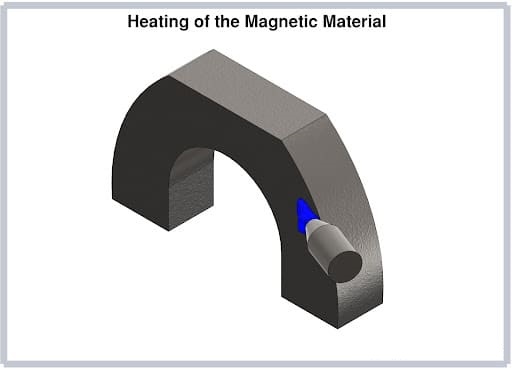
مواد کو گرم کرنا
آئسوسٹیٹک کمپیکشن کے عمل کے بعد پاؤڈر دھات کی سلگ کو ڈائی سے الگ کر کے تندور میں ڈال دیا جاتا ہے۔ سنٹرنگ کمپریسڈ پاؤڈر دھاتوں میں گرمی شامل کرنے کا عمل یا طریقہ ہے تاکہ بعد میں انہیں فیوزڈ، ٹھوس دھات کے ٹکڑوں میں تبدیل کیا جا سکے۔
sintering عمل بنیادی طور پر تین مراحل پر مشتمل ہے. ابتدائی مرحلے کے عمل کے دوران، کمپریسڈ مواد کو بہت کم درجہ حرارت پر گرم کیا جاتا ہے تاکہ تمام نمی یا تمام آلودہ مادوں کو دور کیا جا سکے جو اسوسٹیٹک کمپیکشن کے عمل کے دوران پھنس گئے ہوں۔ سنٹرنگ کے دوسرے مرحلے کے دوران، مرکب کے پگھلنے کے نقطہ کے بارے میں 70-90٪ درجہ حرارت میں اضافہ ہوتا ہے۔ اس کے بعد درجہ حرارت کو گھنٹوں یا دنوں کی جگہ پر رکھا جاتا ہے تاکہ چھوٹے ذرات آپس میں مل جائیں، بانڈ اور فیوز ہو جائیں۔ sintering کا آخری مرحلہ وہ ہوتا ہے جب مواد کو درجہ حرارت کے کنٹرول میں اضافے میں بہت آہستہ سے ٹھنڈا کیا جاتا ہے۔
مواد کی annealing
حرارتی عمل کے بعد اینیلنگ کا عمل آتا ہے۔ یہ تب ہوتا ہے جب sintered مواد ایک اور مرحلہ وار کنٹرول شدہ حرارتی اور کولنگ کے عمل سے گزرتا ہے تاکہ مواد کے اندر رہ جانے والے کسی بھی یا تمام بقایا دباؤ کو ختم کر کے اسے مضبوط بنایا جا سکے۔
میگنیٹ فنشنگ
مندرجہ بالا sintered میگنےٹ مشینی کی کچھ سطح یا ڈگری پر مشتمل ہوتے ہیں، ان کو ہموار اور متوازی پیسنے سے لے کر یا بلاک میگیٹس سے چھوٹے حصوں کی تشکیل تک۔ مقناطیس بنانے والا مواد بہت سخت اور ٹوٹنے والا ہے (Rockwell C 57 سے 61)۔ اس لیے اس مواد کو سلائسنگ کے عمل کے لیے ہیرے کے پہیوں کی ضرورت ہوتی ہے، وہ پیسنے کے عمل کے لیے کھرچنے والے پہیوں کے لیے بھی استعمال ہوتے ہیں۔ سلائسنگ کا عمل بڑی درستگی کے ساتھ کیا جا سکتا ہے اور عام طور پر پیسنے کے عمل کی ضرورت کو دور کرتا ہے۔ چِپنگ اور کریکنگ کو کم کرنے کے لیے مذکورہ بالا عمل کو بہت احتیاط سے کرنے کی ضرورت ہے۔
ایسے معاملات ہیں جہاں مقناطیس کی حتمی ساخت یا شکل روٹی کی روٹیوں جیسے ہیرے کے پیسنے والے پہیے کے ساتھ پروسیسنگ کے لیے بہت موزوں ہے۔ حتمی شکل میں حتمی نتیجہ پیسنے والے پہیے سے گزر جاتا ہے اور پیسنے والا وہیل درست اور درست طول و عرض فراہم کرتا ہے۔ اینیلڈ پروڈکٹ تیار شدہ شکل اور طول و عرض کے اتنا قریب ہے کہ اسے بنایا جانا مطلوب ہے۔ Near net shape وہ نام ہے جو عام طور پر اس حالت کو دیا جاتا ہے۔ ایک آخری اور حتمی مشینی عمل کسی بھی اضافی مواد کو ہٹاتا ہے اور ضرورت پڑنے پر ایک بہت ہموار سطح پیش کرتا ہے۔ آخر میں سطح کو سیل کرنے کے لیے مواد کو حفاظتی کوٹنگ دی جاتی ہے۔
مقناطیسی عمل
مقناطیسی تکمیل کے عمل کی پیروی کرتا ہے، اور جب مینوفیکچرنگ کا عمل مکمل ہو جاتا ہے، تو مقناطیس کو بیرونی مقناطیسی میدان پیدا کرنے کے لیے چارج کرنے کی ضرورت ہوتی ہے۔ اس کو حاصل کرنے کے لئے، solenoid استعمال کیا جاتا ہے. سولینائیڈ ایک کھوکھلا سلنڈر ہوتا ہے جس میں مقناطیس کے مختلف سائز اور شکلیں رکھی جا سکتی ہیں یا فکسچر کے ساتھ سولینائڈ کو مختلف مقناطیسی نمونوں یا ڈیزائن فراہم کرنے کے لیے تیار کیا جاتا ہے تاکہ ان طاقتور میگنےٹس کو ان کے مقناطیسی حالات میں سنبھالنے اور جمع کرنے سے بچنے کے لیے بڑی اسمبلیوں کو میگنیٹائز کیا جا سکے۔ . میگنیٹائزنگ فیلڈ کی ضروریات پر غور کیا جانا چاہئے، جو بہت اہم ہیں۔
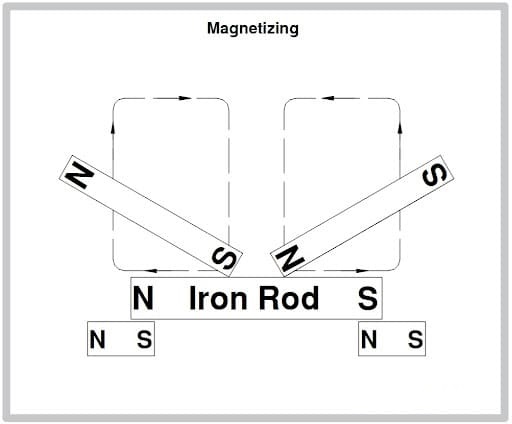
پوسٹ ٹائم: جولائی 05-2022